Exploring 12 Common Sensor Types & Their Impact on Performance, Safety, & Convenience From kitchen appliances to vehicles, electronic sensors have long been essential components inside the devices we enjoy as a society. Sensors are used to detect...
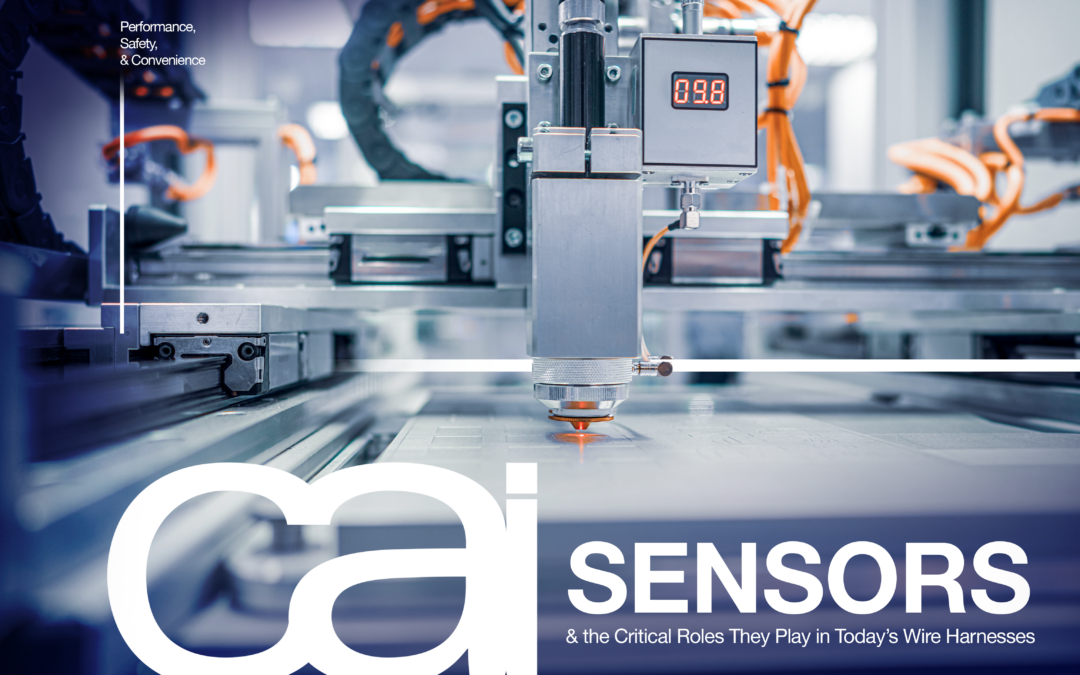
Exploring 12 Common Sensor Types & Their Impact on Performance, Safety, & Convenience From kitchen appliances to vehicles, electronic sensors have long been essential components inside the devices we enjoy as a society. Sensors are used to detect...
Why CAI is Your Wire Harness Cost Savings Solution In the increasingly competitive world of modern manufacturing, wire harnesses are essential components across a broad range of industries, from automotive and aerospace to industrial machinery and consumer...
Intricate Wire Harnesses Require Custom Solutions From Trusted Experts Used in countless electrical applications, wire harnesses come in all shapes, sizes, and complexities. While a “simple” wire harness organizes a handful of wires into a bundle for basic...
Ensuring Optimal Safety in Wire Harness Design The ability to control and utilize electricity — for everything from lighting homes to powering cars — is easily one of history’s greatest achievements, leading to many of our modern conveniences. However, there...
Extreme Conditions Call for Extra Consideration in Wire Harness Manufacturing Wire harnesses must be carefully crafted in order to effectively supply power and data to the machines and devices we use in our homes and businesses every day. The same is true for...
In the world of cable assembly manufacturing, precision and adherence to best practices during every step are essential to ensuring safety, reliability, and optimal performance. Meanwhile, just one mistake can cause disastrous ripple effects throughout production — leading to time and money wasted. Worse yet, it can result in a subpar product that fails in the field.
While rigorous planning combined with extensive experience and skills are needed to design a cable assembly, it also helps to learn from others’ mistakes and be aware of other manufacturers’ shortcomings so as to avoid them.
For over 35 years, our team at CAI has designed and manufactured countless electrical systems for a wide variety of applications in just about every industry, so we’re well aware of what to do and what not to. We pair off-the-shelf solutions with special processes such as overmolding to produce high-quality cable assemblies while avoiding the many mistakes a lesser manufacturer can make, such as these seven common ones:
Choosing the wrong wires, connectors, or other components for a cable assembly is one of the most common and critical errors. From selecting the wrong type or gauge of wire for the current capacity to using incompatible connectors, the wrong components can cause everything from connectivity problems and signal degradation to overheating and system failure.
This is why it’s so important to make sure that the connectors, conductors, and other components correspond with the electrical demands, application, and setting. Utilizing standardized components when possible can make replacements and repairs easier.
When designing a cable assembly, its future environment is a key factor in determining what it needs. From extreme temperatures, to frequent bending and vibration, to water and chemical exposure, the right assembly must be able to withstand conditions that can threaten its structural and signal integrity, which means using the right design and materials, like insulation and jacket, for the job. For instance, when quality waterproofing steps aren’t taken to combat water or proper cable shielding isn’t used to protect against electromagnetic interference (EMI), a cable assembly likely won’t last or perform like it should.
During the design stage, it’s vital to provide accurate measurements and specifications to the manufacturer, in order to ensure the process goes as smoothly as possible and the finished product serves the application correctly. In fact, the more information, the better. Insufficient data and directions make it difficult to achieve optimal design and avoid headaches during production. Providing the basics, including voltage, flexibility, and gauge, at least gives engineers a firm foundation on which to build.
Any time you’re working with complex electrical systems, if you fail to account for rapidly advancing technology, your product may outlive its usefulness much faster than you’d like. By anticipating a cable assembly’s future scalability and potential issues new technologies may cause, you make it easier to perform upgrades and modifications rather than having to completely overhaul the entire system.
There are several valuable processes and solutions that manufacturers can employ to turn an ordinary, everyday cable assembly into a much more durable and dependable one. At CAI, we combine the overmolding process with top off-the-shelf solutions to better guard against environmental threats, increase lifespan, and offer more customization options. We also incorporate off-the-shelf strain relief technologies, such as cable glands and reinforced terminations, to distribute force and mitigate damage for applications where the assembly must endure excessive bending or pulling.
Because high-quality connections are critical to the performance of a cable assembly, the joining methods of crimping and soldering must be done with the utmost care and skill. Poor crimping can result in loose connections while insufficient soldering can cause brittle and unreliable joints. This will only lead to issues down the road, from intermittent connectivity to outright failure. Avoiding this mistake demands expert technicians as well as the best in joining tools and practices.
Depending on a number of factors, such as the assembly’s intended use, future environment, and the regulatory standards to which it must adhere, cable assemblies are put through a wide variety of tests focused on different aspects — including continuity, flex/bend strength, and signal integrity — during both the prototype and post-manufacturing stages. When a defect or other issue is detected, it can be addressed and corrected before going out the door and failing in the field. Neglecting thorough testing, skipping relevant tests, and rushing through the testing stage can easily result in cable malfunction down the road.
These are just some of the common mistakes that can significantly impact a cable assembly’s performance and long-term reliability. Knowing them is the first step to avoiding them.
From cable assemblies to wire harnesses, CAI not only avoids those mistakes but also provides superior solutions for the manufacturing of high-quality electrical systems of all volume types. You can trust us to handle your next project with the precision and professionalism it deserves. Reach out to us today with your unique needs.